Porosity in Welding: Identifying Common Issues and Implementing Ideal Practices for Prevention
Porosity in welding is a prevalent concern that usually goes undetected up until it creates significant troubles with the integrity of welds. This usual issue can endanger the stamina and sturdiness of welded frameworks, posing security dangers and bring about expensive rework. By recognizing the root causes of porosity and implementing effective prevention methods, welders can significantly enhance the high quality and integrity of their welds. In this discussion, we will check out the key elements adding to porosity formation, examine its harmful results on weld efficiency, and talk about the most effective techniques that can be adopted to decrease porosity occurrence in welding processes.
Typical Causes of Porosity
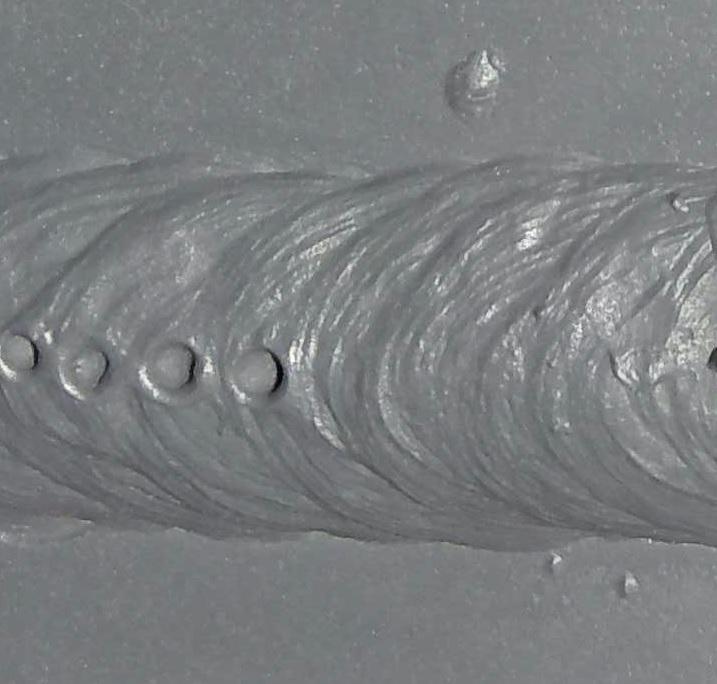
Another regular culprit behind porosity is the existence of pollutants on the surface of the base steel, such as oil, oil, or corrosion. When these impurities are not efficiently removed before welding, they can vaporize and become trapped in the weld, creating problems. Making use of filthy or wet filler products can present contaminations into the weld, contributing to porosity issues. To alleviate these usual reasons for porosity, detailed cleansing of base metals, appropriate securing gas selection, and adherence to optimal welding parameters are crucial practices in attaining top quality, porosity-free welds.
Influence of Porosity on Weld Quality

The existence of porosity in welding can considerably compromise the structural stability and mechanical homes of welded joints. Porosity develops gaps within the weld steel, deteriorating its total toughness and load-bearing capability. These voids serve as stress and anxiety focus factors, making the weld extra susceptible to fracturing and failing under used lots. In addition, porosity can reduce the weld's resistance to rust and various other ecological factors, better decreasing its durability and performance.
One of the key effects of porosity is a decrease in the weld's ductility and toughness. Welds with high porosity levels often tend to show lower impact stamina and minimized ability to deform plastically before fracturing. This can be specifically concerning in applications where the welded components undergo vibrant or cyclic loading conditions. Furthermore, porosity can restrain the weld's ability to efficiently transfer pressures, causing premature weld failure and prospective safety and security threats in vital frameworks.
Ideal Practices for Porosity Avoidance
To enhance the structural honesty and quality of welded joints, what specific actions can be applied find more to reduce the occurrence of porosity during the welding procedure? Porosity prevention in This Site welding is essential to ensure the honesty and toughness of the final weld. One efficient method appertains cleansing of the base metal, eliminating any impurities such as corrosion, oil, paint, or moisture that can cause gas entrapment. Guaranteeing that the welding devices remains in excellent condition, with tidy consumables and ideal gas circulation rates, can likewise significantly reduce porosity. Furthermore, maintaining a secure arc and managing the welding specifications, such as voltage, existing, and travel speed, assists produce a consistent weld swimming pool that lessens the risk of gas entrapment. Making use of the correct welding strategy for the details material being bonded, such as changing the welding angle and weapon setting, can even more stop porosity. Normal examination of welds and immediate remediation of any type of concerns identified throughout the welding process are essential techniques to stop porosity and produce top notch welds.
Relevance of Proper Welding Strategies
Implementing correct welding techniques is critical in making certain the architectural integrity and quality of bonded joints, constructing upon the structure of reliable porosity avoidance actions. Welding techniques directly impact the overall stamina and longevity of the welded framework. One vital facet of appropriate welding techniques is keeping the appropriate heat input. Extreme warm can lead discover this info here to raised porosity due to the entrapment of gases in the weld swimming pool. On the other hand, not enough warm may lead to incomplete combination, creating possible powerlessness in the joint. In addition, utilizing the appropriate welding parameters, such as voltage, current, and take a trip speed, is critical for accomplishing sound welds with minimal porosity.
Moreover, the selection of welding process, whether it be MIG, TIG, or stick welding, need to line up with the specific requirements of the job to guarantee optimum outcomes. Appropriate cleansing and prep work of the base steel, in addition to picking the ideal filler material, are additionally important elements of skillful welding methods. By adhering to these best techniques, welders can lessen the threat of porosity formation and create high-grade, structurally audio welds.
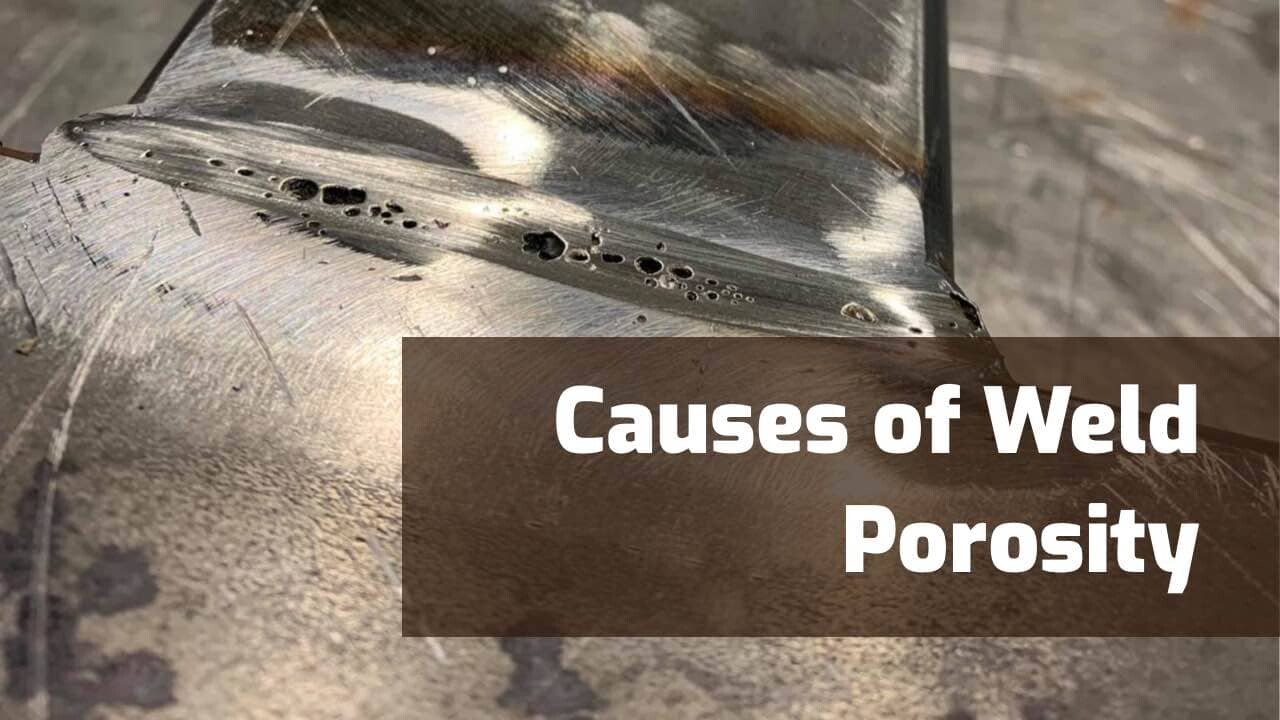
Checking and High Quality Control Actions
Examining procedures are important to detect and prevent porosity in welding, ensuring the strength and durability of the final product. Non-destructive testing techniques such as ultrasonic screening, radiographic testing, and aesthetic assessment are typically employed to recognize possible problems like porosity.
Post-weld evaluations, on the various other hand, examine the final weld for any kind of defects, consisting of porosity, and confirm that it satisfies specified requirements. Applying a comprehensive quality control plan that includes thorough testing procedures and assessments is paramount to minimizing porosity issues and ensuring the total top quality of bonded joints.
Conclusion
Finally, porosity in welding can be a common issue that impacts the quality of welds. By determining the common root causes of porosity and executing finest techniques for avoidance, such as proper welding methods and testing procedures, welders can make certain top quality and trustworthy welds. It is vital to focus on avoidance techniques to lessen the occurrence of porosity and preserve the honesty of bonded structures.